انواع کمپرسور های برودتی | کمپرسور سردخانه
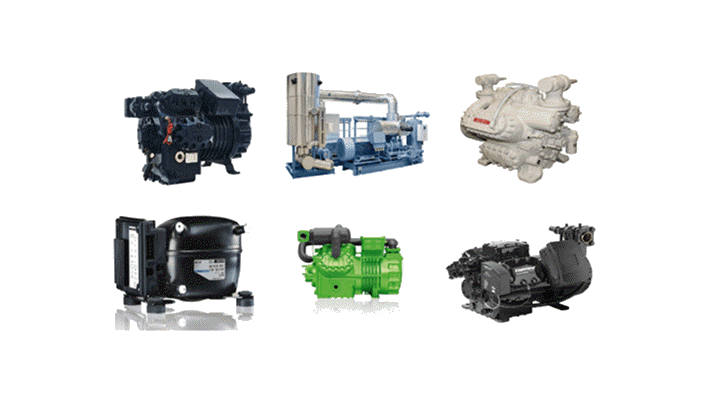
کمپرسورها دستگاه هایی هستند که با صرف انرژی ، سیالات را فشرده کرده و حرکت می دهند. در اثر این عملیات، گاز متراکم شده و دمای آن به شدت بالا می رود. در سیستم های برودتی گاز خارج شده از کمپرسور در مسیر خود از یک مبدل حرارتی (کندانسور) عبور کرده تا حرارت خود دست داده و بتواند در اواپراتور سرما تولید کند. کمپرسورها انواع مختلف و کاربردهای متنوعی دارند.
تاریخچه کمپرسور و سیستم های سرمایش
اگر کمپرسور برودتی را وسیلهای درنظر بگیریم که گاز را فشرده میسازد، با این تعبیر انسان از 5 هزار سال قبل از میلاد مسیح از فشرده سازها برای کارهای خود استفاده میکرده است. درواقع آنها زمانی که شروع به ذوب فلزات کردند، از دمندهها برای فشرده کردن گاز و دمیدن آن به سمت شعله استفاده میکردهاند.
اما در سال 1758 بنجامین فرانکلین توانست با استفاده از یک دمنده و الکل، دمای یک جسم را کاهش دهد. او هوای فشرده را با استفاده از یک دمنده از روی الکل عبور داد. با این کار او توانست دما را تا دمای یخ زدن کاهش دهد. در واقع با انجام این کار، سیستمهای خنک سازی مکانیکی پایه گذاری شدند.
پس از آن، آمونیاک اولین ماده مبردی بود که برای فرآیند کاهش دما استفاده شد. در اواسط قرن نوزدهم، تقریبا چیزی مشابه با سیکلهای تبرید امروزی ساخته شد که مایع کم فشار با دریافت گرما به گاز تبدیل میشد. سپس این گاز با یک کمپرسور فشرده شده و بعد از آن در یک کندانسور، دمای آن کاهش پیدا میکرد و دوباره به مایع تبدیل میشد. در طی سال های بعد، فناوری ساخت کمپرسورها پیشرفت پیدا کرد و کمپرسورهایی پیچیدهتر و با بازدهی بیشتری نسبت به کمپرسورهای پیستونی ساخته شدند.
نحوه کار کمپرسورها
برای درک بهتر کاری که کمپرسور انجام میدهد، باید نسبت به سیکلهای تبرید شناخت پیدا کرد. به همین منظور پیشنهاد میکنیم مقاله سیکل تراکمی سرمایش سردخانه را در وبسایت شرکت دامون مطالعه کنید. زمانی که کمپرسور شروع به کار میکند، ماده مبرد که فشار پایینی دارد را از اوپراتور میگیرد. ماده مبردی که از اوپراتور مکیده میشود، درواقع حامل گرمای جذب شده از سردخانه است و باید به نحوی این انرژی به محیط بیرون منتقل شود. اما تبادل گرما زمانی اتفاق میافتد که دمای گاز از دمای محیط بیشتر باشد. کمپرسور با کاهش حجم گاز، باعث افزایش فشار گاز میشود و در نتیجه دمای گاز نیز افزایش پیدا میکند. پس از افزایش دمای ماده مبرد، کمپرسور به عنوان یک پمپ عمل کرده و این گاز گرم را به کندانسور میفرستد تا در آنجا دمای آن کاهش پیدا کند.
کاربرد کمپرسور ها
کمپرسورها را میتوان در صنایع و مصارف خانگی برای استفادههای گوناگون پیدا کرد. از باد کردن تایر خودرو گرفته تا ساخت یخچالها و چیلرهای بزرگ، در تمامی این سیستمها از کمپرسورها استفاده میشود. در خطوط انتقال گاز نیز میتوان از کمپرسور های برودتی استفاده کرد تا بتوان گاز را در طول لوله به مسافتهای دور انتقال داد. در سیستمهای سرمایش خانگی و یخچالهای خانگی نیز کمپرسورها مهمترین نقش را ایفا میکنند.
موتورهای جت نیز برای کار کردن نیاز به نوعی از کمپرسور به نام کمپرسورهای محوری دارند که در ادامه نحوه کار آنها توضیح داده شده است. در خودروهای امروزی نیز از نوعی از کمپرسورها برای فشرده سازی هوای ورودی به سیلندر استفاده میشود تا کارایی موتور افزایش پیدا کند. دامنه استفاده از کمپرسورها به همین موارد ختم نمیشود و کمپرسورها را میتوان در بسیاری از موارد زندگی روزمره نیز مشاهده کرد.
انواع کمپرسور
انوع گوناگونی از کمپرسور وجود دارد که در ابتدا ممکن است افراد را سردرگم کند. بنابراین دسته بندیهای مختلفی برای گروهبندی کمپرسورها ارائه شدهاند که میتواند در انتخاب درست به کار آیند. به طور کلی کمپرسورها را با ویژگیهای زیر دسته بندی میکنند:
- سرعت (سرعت ثابت یا سرعت متغییر)
- تعداد مراحل کار (تک مرحلهای، دو مرحلهای و چند مرحلهای)
- سیستم قدرت
- ساختار (باز، سمی هرمتیک و هرمتیک)
- سیستم خنکسازی کمپرسور (هوا، آب و روغن)
- روشهای روانکاری کمپرسور
با این حال موارد بالا برای دسته بندی کامل کمپرسور برودتی کافی نیستند. به طور معمول کاربردیترین دسته بندی برای کمپرسور، به نحوه کار آنها برمیگردد. برای افزایش فشار یک سیال میتوان از دو روش استفاده کرد: کاهش حجم و یا افزایش سرعت. کمپرسورهایی که از روش اول استفاده میکنند را کمپرسورهای جابهجایی مثبت (Positive displacement) و کمپرسورهایی که سرعت سیال را افزایش میدهند را کمپرسورهای دینامیک (Dynamic) مینامند.
انواع کمپرسور های برودتی:
کمپرسورهای پیستونی
کمپرسورهای اسکرو
کمپرسورهای اسکرال
کمپرسورهای روتاری
کمپرسور سانتریفیوژ
کمپرسور سمی هرمتیک
کمپرسور پیستونی (رفت و برگشتی)
دامنه استفاده از کمپرسور پیستونی بسیار گسترده است و برای کاربردهای مختلفی از آنها استفاده میشود. در این کمپرسور همانند موتور ماشین از پیستون و سیلندر استفاده میشود. حرکت رفت و برگشتی پیستون که توسط یک عامل متحرک خارجی ایجاد میشود، ماده مبرد را فشرده میسازد. این کمپرسورهای میتوانند یک یا چند سیلندر داشته باشند.
کمپرسورهای پیستونی نیز خود به سه دسته هرمتیک، سمی هرمتیک و باز تقسیم بندی میشوند.
قطعات کمپرسور پیستونی
سیلندر، پیستون، رینگ پیستون، شاتون، میل لنگ، دریچه ورودی و دریچه خروجی از مهمترین قطعات یک کمپرسور رفت و برگشتی هستند. سیلندر کمپرسورهای کوچک را معمولا از جنس چدن میسازند. در کمپرسورهای تک سیلندر، سیلندر و بدنه کمپرسور یکپارچه هستند ولی در کمپرسورهای چند سیلندری، ابتدا سیلندرها ساخته میشوند و سپس در کنار یکدیگر در بدنه قرار میگیرند.
همانند موتور اتوموبیل، پیستون وظیفه حرکت در طول سیلندر را دارد و با حرکت خطی خود، گاز را فشرده میکند. پیستونها را نیز مانند سیلندر معمولا از جنس چدن یا آلومینیوم میسازند. در طول حرکت پیستون، ماده مبرد نباید از منافذ میان پیستون و سیلندر عبور کند و به همین علت از رینگ پیستون برای جلوگیری از این اتفاق استفاده میشود. البته در کمپرسورهای کوچک نیازی به استفاده از رینگ پیستون نیست و روغن موجود در محفظه سیلندر، از نفوذ ماده مبرد به قسمت پایین پیستون جلوگیری میکند.
میل لنگ در کمپرسور وظیفه دارد که حرکت دورانی موتور الکتریکی را به پیستون منتقل کند. موتور الکتریکی میتواند به صورت مستقیم به میل لنگ متصل شود یا اینکه به وسیله یک تسمه، نیروی موتور به این میله منتقل میشود. درنهایت میل لنگ به وسیله شاتون به پیستون متصل میشود و به این ترتیب پیستون به حرکت در میآید.
کمپرسور اسکرو
این کمپرسور از یک جفت روتور پیچیشی تشکیل میشود که ماده مبرد در بین این دو قرار میگیرد و فشرده میشود. کمپرسور اسکرو توانایی این را دارد که برای مقادیر کم گاز نیز فشارهای بالایی تولید کنند. کمپرسورهای پیچشی به طور معمول مصرف انرژی کمتری نسبت به کمپرسور پیستونی دارند و میتوانند به طور مداوم کار کنند.
کمپرسور اسکرال
کمپرسور اسکرال دارای تکنولوژی جدیدتری نسبت به دیگر کمپرسورهای این لیست هستند. در داخل این فشردهساز، یک حلزونی ثابت قرار دارد که به آن اسکرال گفته میشود. در کنار این اسکرال، حلزونی دیگری نیز وجود دارد که حول آن میچرخد. در حین چرخیدن حلزونی دوم، ماده مبرد به سمت مرکز حرکت میکند و فشرده میشود. به دلیل اینکه کمپرسورهای اسکرال قطعات متحرک زیادی ندارند، به سرعت در حال محبوب شدن هستند؛ چراکه با کمتر بودن قطعات متحرک، احتمال خرابی کمپرسور نیز کمتر میشود.
کمپرسور روتاری
کمپرسور روتاری معمولا کوچک و کم سر و صدا هستند و بنابراین در مکان هایی که نیاز به کم بودن سر و صدا باشد، استفاده میشوند. انوع گوناگونی از کمپرسور روتاری وجود دارد ولی اساس عملکرد آنها یکسان است. در کمپرسور روتاری از یک شفت در میانه آنها استفاده میشود که بر روی این شفت پره های زیادی قرار دارد. با ورود گاز به محفظه کمپرسور و حرکت پرهها، ماده مبرد فشرده میشود. در نوع دیگری از کمپرسور روتاری، پره روی شفت قرار ندارد و بر روی محفظه کمپرسور قرار میگیرد.
کمپرسور سانتریفیوژ
در کمپرسور گریز از مرکز از دو دمنده یا پروانه استفاده میشود که میتوانند حجم زیادی از گاز را فشرده کنند. این کمپرسورها جزو دسته کمپرسورهای دینامیکی محسوب میشوند چراکه اساس کار آنها، تغییر انرژی جنبشی گاز است. سپس با استفاده از یک دیفیوزر، این انرژی جنبشی به فشار استاتیکی یا انرژی پتانسیل تبدیل میشود.
تفاوت انواع کمپرسور چیلر، سردخانه و سیستمهای سرمایشی
انواع کمپرسور های برودتی که در بالا ذکر شدند بسته به کاربرد میتوانند در چیلر و سردخانه مورد استفاده قرار بگیرند. درچیلرها معمولا برای خنک سازی آب در ابعاد کوچک (ظرفیتی کمتر از 200 تن) از کمپرسورهای اسکرال استفاده میشود. ظرفیت این کمپرسورها معمولا از 20 تن شروع میشود. برای افزایش ظرفیت سیستمهایی که از کمپرسور های اسکرال استفاده میکنند، باید تعداد کمپرسور را افزایش داد. ضعف این موضوع در این است که ظرفیت چیلر را تنها میتوان به صورت پلهای افزایش داد و لزوما نمیتوان به ظرفیت کاملا دلخواه رسید. اما مزیت این شیوه در این است که اگر یکی از کمپرسورها خراب شود، با اینکه ظرفیت سیستم کاهش پیدا میکند، اما سیستم به طور کامل قطع نمیشود.
به طور معمول حداکثر از 6 کمپرسور 30 تنی اسکرال در کنار هم استفاده میشود و برای ظرفیتهای بیشتر باید از کمپرسورهای اسکرو استفاده کرد. چنین کمپرسورهایی میتوانند تا 500 تن ظرفیت داشته باشند. برای این کمپرسورها این قابلیت وجود دارد که میتوان ظرفیت کاری آنها را بین بازه 20 درصد تا 100 درصد تنظیم کرد و بنابراین میتوان ظرفیت دلخواه را به طور دقیق به دست آورد. کمپرسورهای اسکرو بازده بالایی به نسبت دیگر کمپرسورهای معمول دارند اما صدایی که تولید میکنند از کمپرسورهای اسکرال بیشتر است.
کمپرسور سمی هرمتیک
کمپرسور برودتی دیگری که برای سیستمهای سرمایش استفاده میشود، کمپرسور گریز از مرکز (سانتریفیوژ) است. با استفاده از پرههای ورودی میتوان ظرفیت این نوع از کمپرسور را تغییر داد. همچنین میتوان از یک درایو فرکانس متغییر (VFD) برای تغییر سرعت پروانه کمپرسور استفاده کرد و به این ترتیب میتوان ظرفیت کمپرسور را افزایش یا کاهش داد.
پرکاربردترین کمپرسور برای یخچالها و فریزهای خانگی، آب سردکنها و… ،کمپرسورهای پیستونی محسوب میشوند. برای مصارف خانگی، از کمپرسورهای پیستونی هرمتیک استفاده میشود و برای مصارف صنعتی، کمپرسورهای باز و نیمه هرمتیک استفاده میشوند. ظرفیت کمپرسورهای پیستونی از 0.5 تن میتواند آغاز شود و تا 150 تن نیز میتواند افزایش پیدا کند. در کمپرسورهای چند سیلندره، ظرفیت کمپرسور با استفاده از روشن و خاموش کردن سیلندرها تغییر پیدا میکند. مهمترین مزیت کمپرسورهای پیستونی، قیمت پایین است که آنها را برای مصارف خانگی مناسب میکند. البته این کمپرسور های سردخانه سر و صدای زیادی تولید میکنند و مسائل روغن ریزی نیز در آنها شایع است. درضمن معمولا کمپرسورهای پیستونی بازده پایین دارند و برای افزایش کارایی سیستم، باید از دیگر کمپرسورها استفاده کرد.
مقایسه کمپرسورها
تفاوت کمپرسور هرمتیک، سمی هرمتیک و باز چیست؟
در کمپرسورهای هرمتیک، موتور و کمپرسور هر دو در یک محفظه استیل قرار گرفتهاند و درواقع در داخل این محفظه پلمپ شدهاند. در این صورت کمپرسور از خطر نشتی در امان میماند ولی درصورت خرابی قطعات داخلی، قابل تعمیر نیست.
در کمپرسورهای سمی هرمتیک نیز مانند مدلهای هرمتیک موتور و کمپرسور در داخل یک محفظه قرار میگیرند. اما این کار به نحوی صورت میگیرد که درصورت خرابی قطعات داخلی، امکان دسترسی به آنها و تعمیر کردنشان وجود دارد.
سیستمهای فشرده سازی باز مانند سیستم تهویه خودرو، بیشتر در معرض نشت هستند. در این کمپرسور های برودتی ، روغن از نشت گاز جلوگیری میکند و درصورتی که کمپرسور برای مدت طولانی مورد استفاده قرار نگیرد، روغن بخار میشود و در محلهای بسته شدن بدنه کمپرسور، نشتی به وجود میآید و بعد از مدتی سیستم باید دوباره شارژ شود.
طول عمر کمپرسورهای هرمتیک معمولا 2 تا 3 سال است (البته در مواردی میتواند تا بیش از 3 سال هم عمر کند) و پس از خراب شدن آنها، باید با کمپرسور جدیدی جایگزین شوند. درحالی که نمونههای سمی هرمتیک طول عمری بین 3 تا 10 سال دارند که بسته به نوع استفاده، این مقدار میتواند به بیش از ده سال نیز ادامه پیدا کند.
کمپرسورهای هرمتیک با اینکه معایب زیادی دارند، اما قیمت تمام شده سیستم را پایین میآورند. همچنین در مواردی که هزینه تعمیر به نسبت ارزش کمپرسور بیشتر میشود، استفاده از نمونههای هرمتیک به صرفهتر خواهد بود و جایگزینی یک نمونه جدید دردسر کمتری نسبت به تعمیر کمپرسور دارد.
تفاوت کمپرسور تک مرحلهای، دو مرحلهای و چند مرحلهای
بیشتر کمپرسورهایی که پیش از این به آنها اشاره شد، در در دو نوع تک مرحله و چند مرحلهای ساخته میشوند. زمانی که گاز فشرده میشود، دمای آن افزایش پیدا میکند. مزیت استفاده از کمپرسورهای چند مرحلهای این است که به گاز اجازه میدهد در بین هر مرحله خنک شود و درنتیجه این موضوع، بازده کلی سیستم افزایش پیدا میکند.
البته کمپرسورهای چندمرحلهای تنها برای افزایش بازده سیستم استفاده نمی شوند؛ در برخی از سیستمها، برای افزایش زیاد فشار، دما به مقداری افزایش پیدا میکند که از محدوده تحمل قطعات داخلی کمپرسور خارج میشود و در این صورت، با چند مرحلهای شدن فرآیند فشردهسازی، میتوان در بین مراحل، دمای گاز را کاهش داد.
همانطور که مشخص است، کمپرسورهای چند مرحلهای پیچیدگی بیشتری در طراحی دارند و درنتیجه قیمت کلی آنها به نسبت کمپرسورهای تک مرحلهای بسیار بیشتر است. به همین دلیل کمپرسورهای تک مرحلهای برای مقیاسهای کوچک و تغییر فشارهای کوچک، گزینه مقرون به صرفهتری محسوب میشوند.
روغن کمپرسور
روغن کمپرسور برودتی چندین نقش مختلف را به طور همزمان انجام میدهد و البته که مهمترین وظیفه آن، روانکاری قطعات است. اما در عین حال در برخی سیستمها از روغن به عنوان خنککننده نیز استفاده میشود. همچنین همانطور که پیش از این نیز گفته شد، در کمپرسورهای باز، روغن وظیفه جلوگیری از وقوع نشتی را ایفا میکند. با این حساب، باید در انتخاب روغن برای کمپرسور دقت زیادی داشت و پیشنهادات تولید کننده را باید در این امر در نظر گرفت.
روغن های کمپرسور معمولا از ترکیبی خاص از روغن های معمول و چند افزودنی تشکیل میشود که در عین حال که قطعات را روان کاری میکند، سازگار با ماده مبرد نیز باشد. اگر روغن و ماده مبرد کوچکترین ناسازگاری داشته باشند، ممکن است صدمات زیادی به قطعات مختلف سیستم تبرید وارد شود.
بخش بزرگی از روغن های کمپرسورها را مواد غیرطبیعی تشکیل دادهاند. همین ویژگی به این روغنها این قابلیت را میدهد که طول عمر بیشتری داشته باشند و مقاومت بیشتری به نسبت روغنهای معدنی در برابر شرایط سخت داشته باشند. در بیش تر سیستمهای سرمایش خانگی از گاز R-410a به عنوان ماده مبرد استفاده میشود و در کنار این ماده، از روغن های پلی استری برای روانکاری قطعات استفاده میشود که در عین حال در ماده مبرد نیز حل نمیشود.
اگرچه سازگاری روغن و ماده مبرد یکی از مهمترین فاکتورهای مربوط به روانکارها محسوب میشود، اما نکات مهم دیگری نیز در مورد آنها وجود دارد. به عنوان مثال رطوبت میتواند برای بعضی از روغنهای غیرطبیعی بسیار زیان آور باشد؛ چراکه رطوبت با برخی از مواد موجود در روغن واکنش داده و تشکیل اسید میدهد. در نتیجه این موضوع، گرانروی و خاصیت روانکاری روغن دستخوش تغییر میشود. درنهایت، چنین اتفاقی میتواند سبب از کار افتادن کمپرسور شود.